In the battle against a new unseen enemy, textile company Yibin Grace wasted no time in manufacturing the scarce essential good – masks.
After running the gauntlet to ensure that they had all the necessary Lunar New Year decorations and foodstuff, few Chinese would have expected to be braving long, snaking queues again so quickly.
But just a few days into the festivities, a time when streets were supposed to be quieter than usual, people across China were out and about, scrambling to get medical masks because of the Covid-19 outbreak.
Even though China may be the manufacturing capital of the world, many people went home empty-handed.
“When the outbreak took place, many places in Chongqing ran out of masks. Even online stores were out of stock,” recalls Jackie Jiang, the team leader of Institutional Banking at DBS Chongqing.
“The situation was dire. Everyone was panicking. Because the virus is extremely contagious and harmful, my family members were very anxious about the shortage of protective equipment and how that might affect the elderly and children.”
Rising to meet the challenge of the mask shortage were domestic companies from all fields. Even the aircraft company that manufactures China’s stealth fighter jets repurposed their factories to produce masks.
Over in Chongqing, textile manufacturer Yibin Grace was designated by the central government as the only state-owned enterprise in Sichuan province to produce medical and anti-epidemic materials. But to do so, the company needed to import a massive amount of raw material that is scarce in China.
“The core raw material of our non-woven medical masks is a special pulp produced overseas, especially in areas like South America. The wood pulp they sell is of good quality and affordable pricing,” explains Mr Li Songgang, deputy director of finance at Yibin Grace.
“Besides the fact that this material is difficult to obtain in China, we were also worried that the epidemic will eventually impact international shipping, which would in turn affect our production capability. This is why we needed to purchase such a large volume and be prepared for the long-term.”
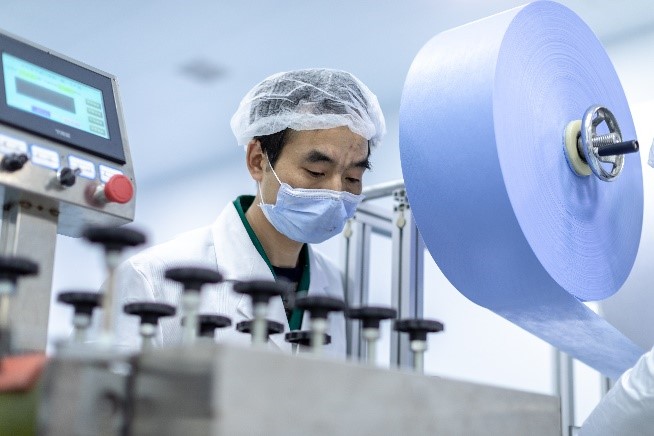
An unassuming piece of fabric during normal times; a life-saving equipment in emergencies.
No time to waste
Faced with the need for additional funds, the company sought the assistance of the DBS Chongqing branch. This was the first case that the bank undertook in the fight against the pandemic in China.
When Jackie received the call from Yibin Grace, she immediately knew she had her work cut out for her. Her primary concern was that the work-from-home protocol would impede the efficiency of what is already a long approval process for such a request.
One of the first things she did was to set up a WeChat group with her colleagues from Global Transaction Services and the operations department where they brainstormed about possible solutions.
After deciding on an action plan, about a dozen bank employees set out to complete their respective tasks, such as helping the client apply for credit, working with the bank’s Chief Operating Officer to get a drawdown quota, reviewing supporting documents and even contacting branches in other cities for assistance.
Because of the tireless work of these bank staff, what would have usually taken seven days was done in just two. This feat was also due to the bank’s prompt activation of multiple nationwide “green channels” that streamlined the approval process, allowing credit loans and remittance services for companies involved in epidemic prevention to be expedited.
Besides receiving a loan of nearly US$10 million to purchase the special wood pulp, Yibin Grace was also issued a bank acceptance bill worth 30 million yuan for mask production purposes.
Because of this injection of funds, the company was able to produce hundreds of thousands of masks within weeks. In the initial stages of the outbreak, most of these masks were deployed by the Sichuan provincial government to frontline medical workers, reducing their risk of infection as they laboured to save lives.
Today, even as the outbreak has come under control in China, the company continues to produce a whopping 1.2 million face masks per day to help the 81 million Sichuan residents stay protected against the virus.
“We all had to work overtime. The WeChat group we were in had hundreds of text and voice messages,” recalls Frank Jiang, a DBS staff who was involved in this particular assignment.
“The job was tough, and it was made harder by not being able to communicate with other colleagues in person,” he adds.
Besides the bank staff, the speedy approval process also surprised the client.
“In these extraordinary times, the work efficiency and professionalism of the bank’s front, middle and back office staff, as well as the strong support by the head office and branch departments have impressed our company,” says Mr Li.
“I would like to extend my thanks for all the help provided. The company is certainly looking forward to having more in-depth cooperation with the bank in the future.”